Our tool for managing your permission to our use of cookies is temporarily offline. Therefore some functionality is missing.
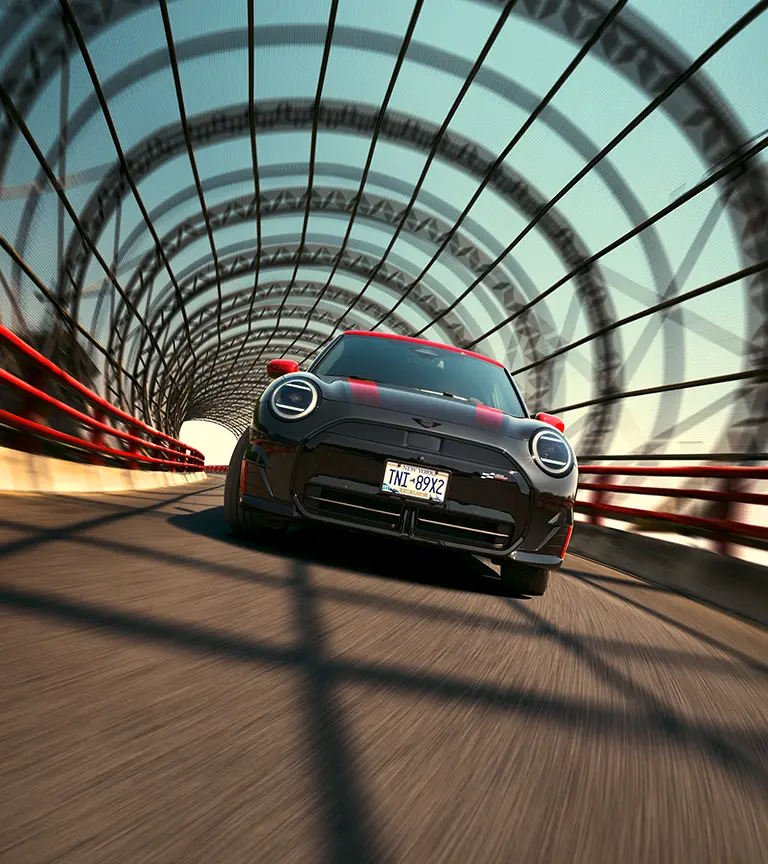
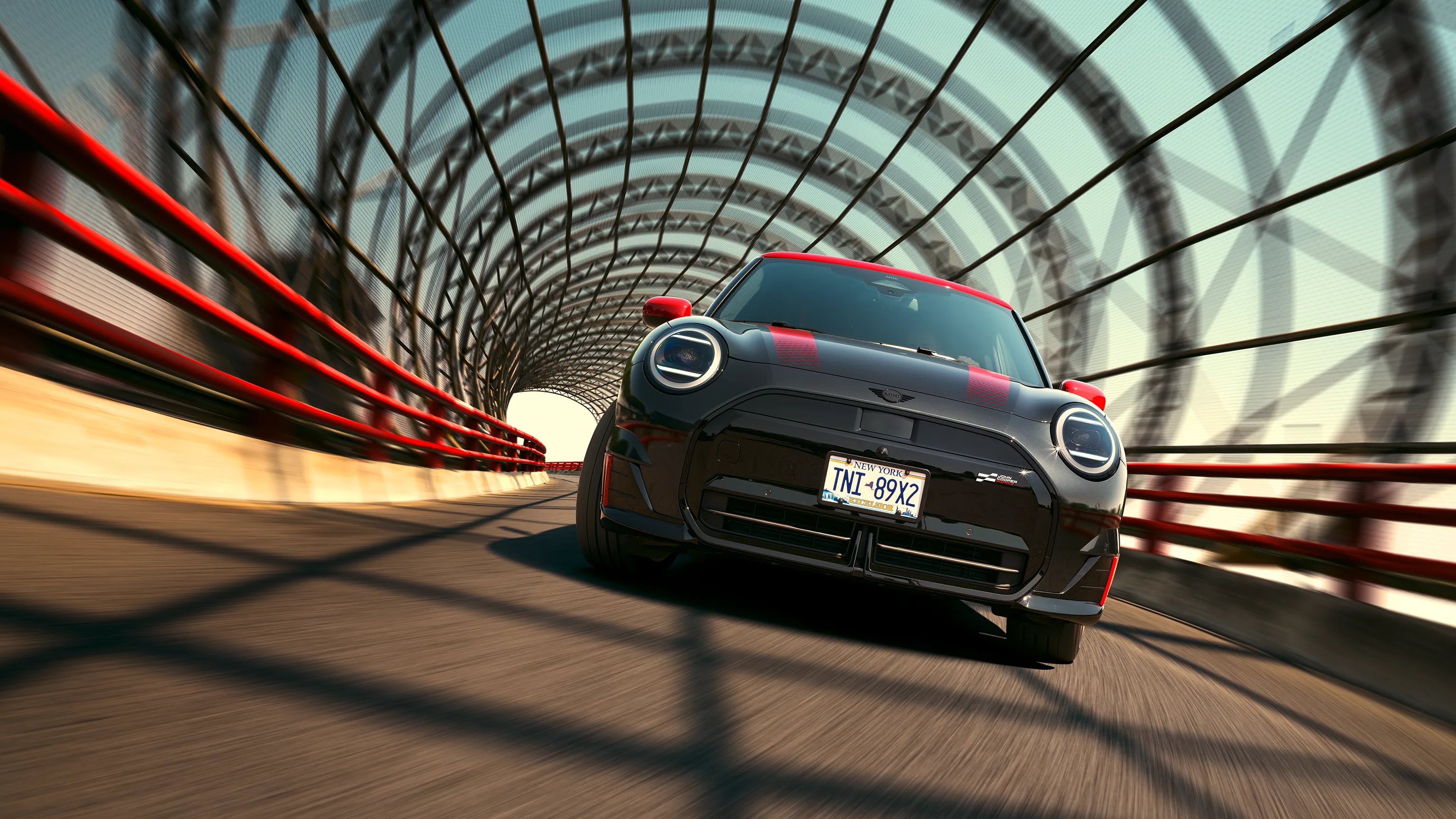
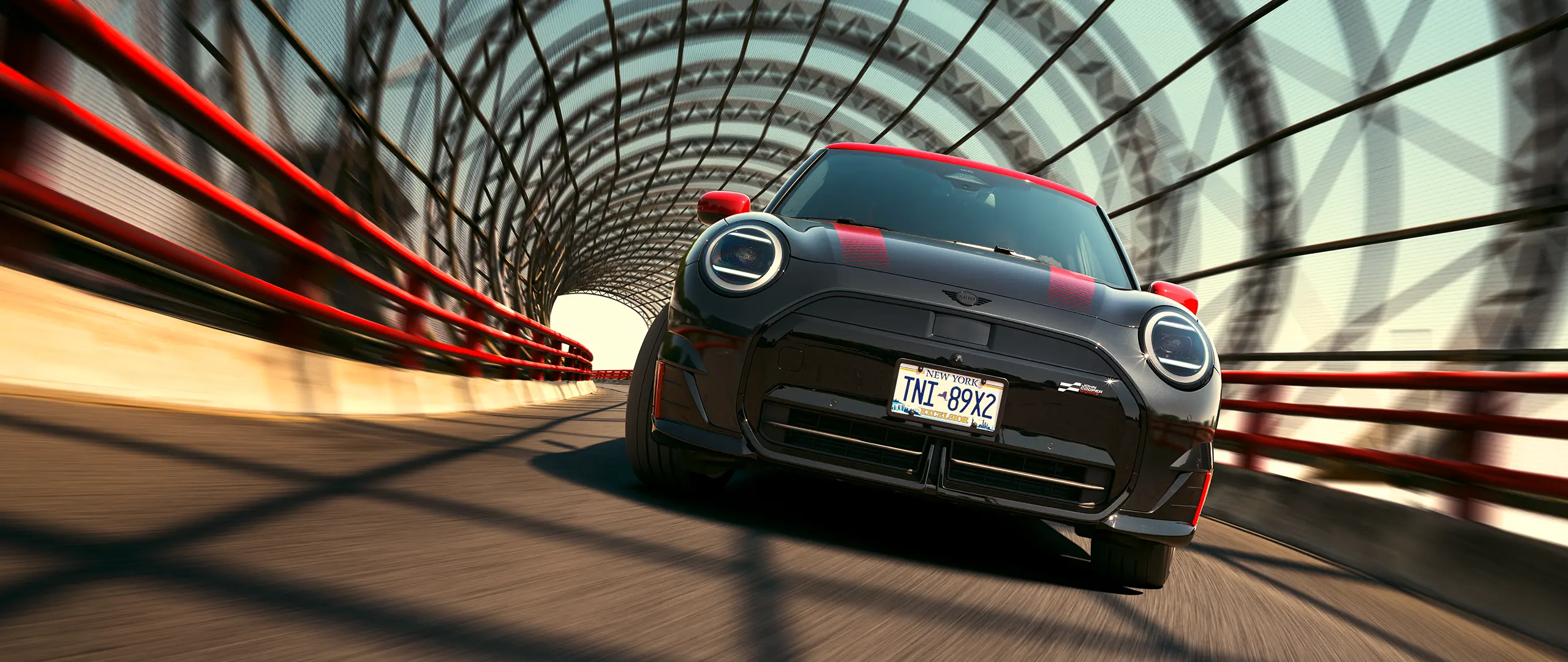
MINI JOHN COOPER WORKS PACK.NICE TO MEET YOU AGAIN.
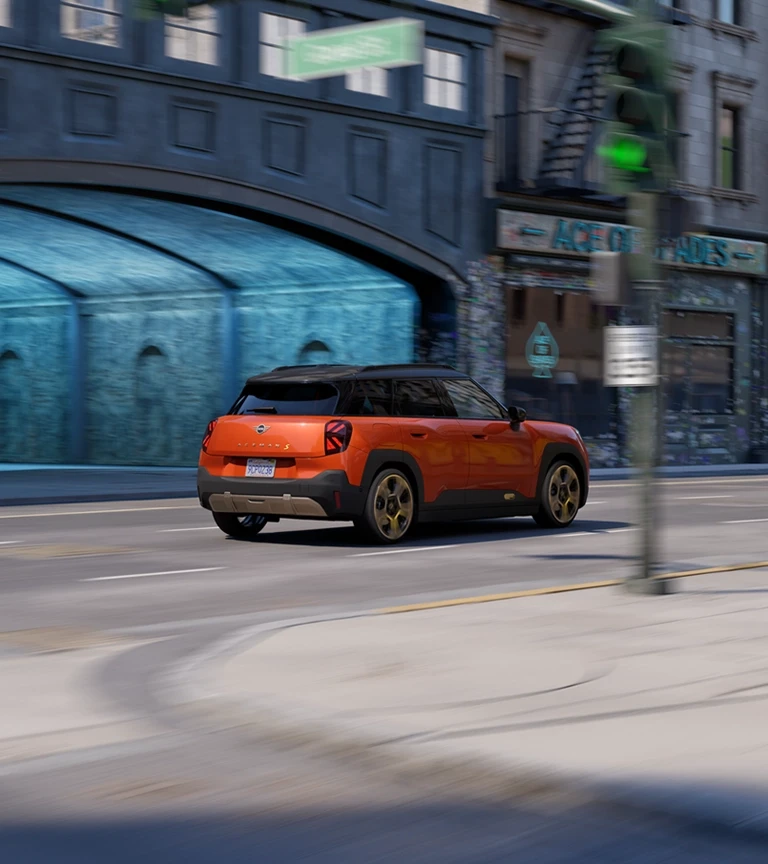
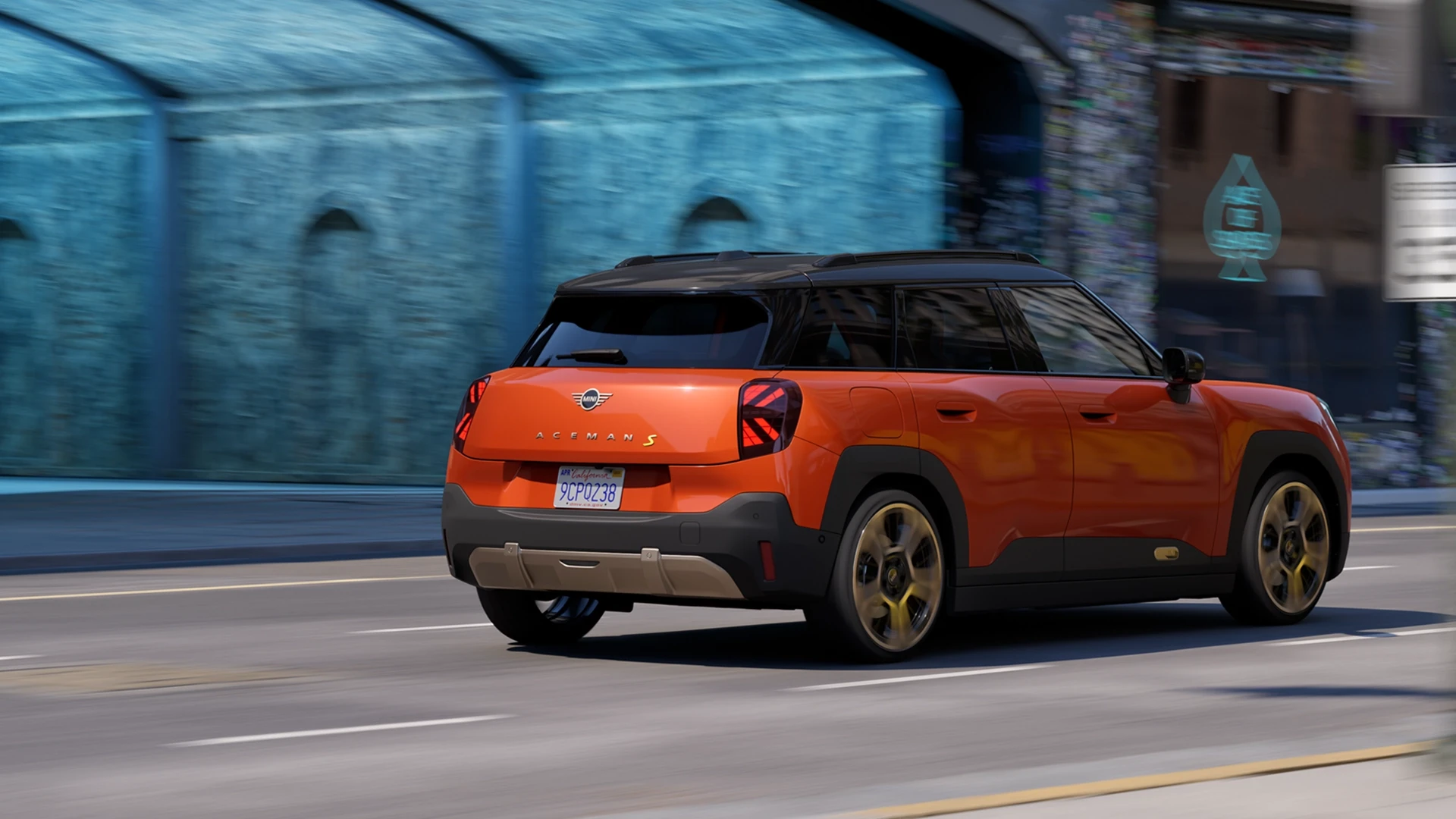
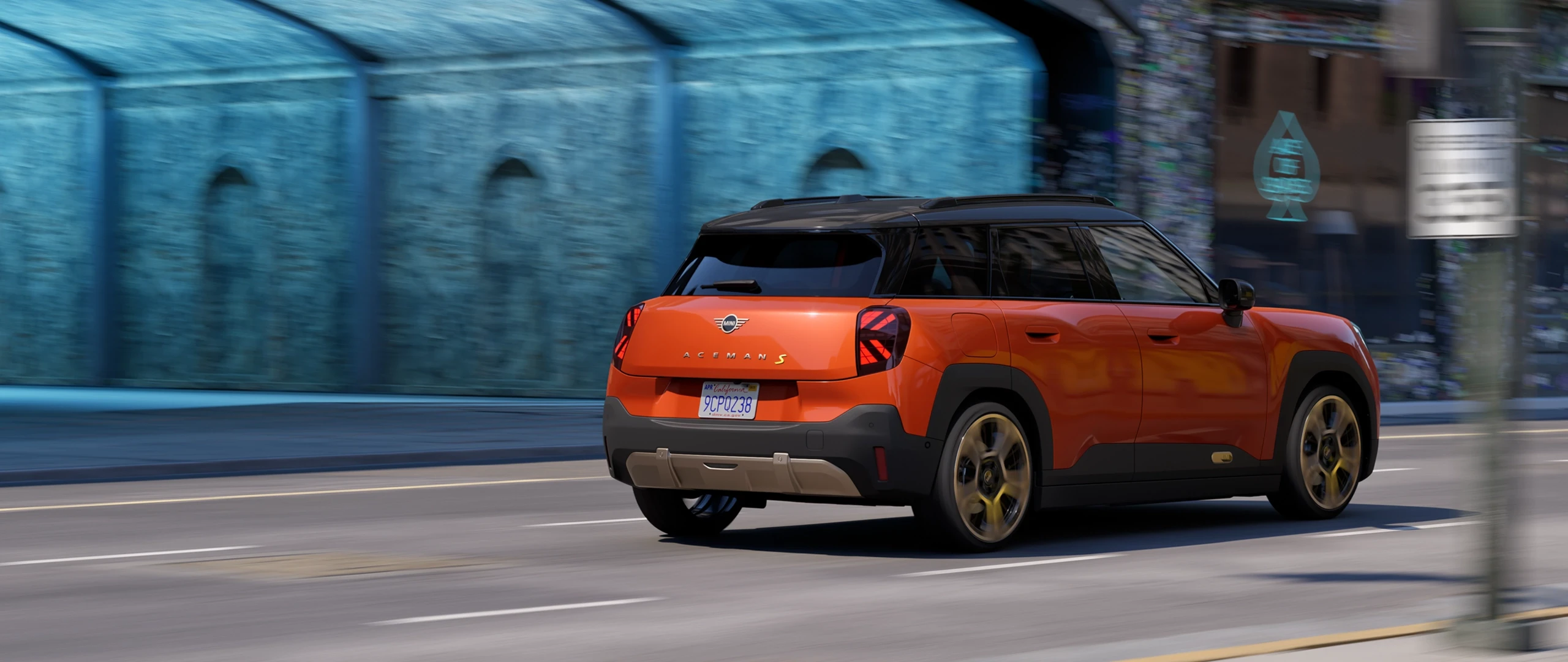
ALL-ELECTRIC MINI ACEMAN.NICE TO MEET YOU AGAIN.
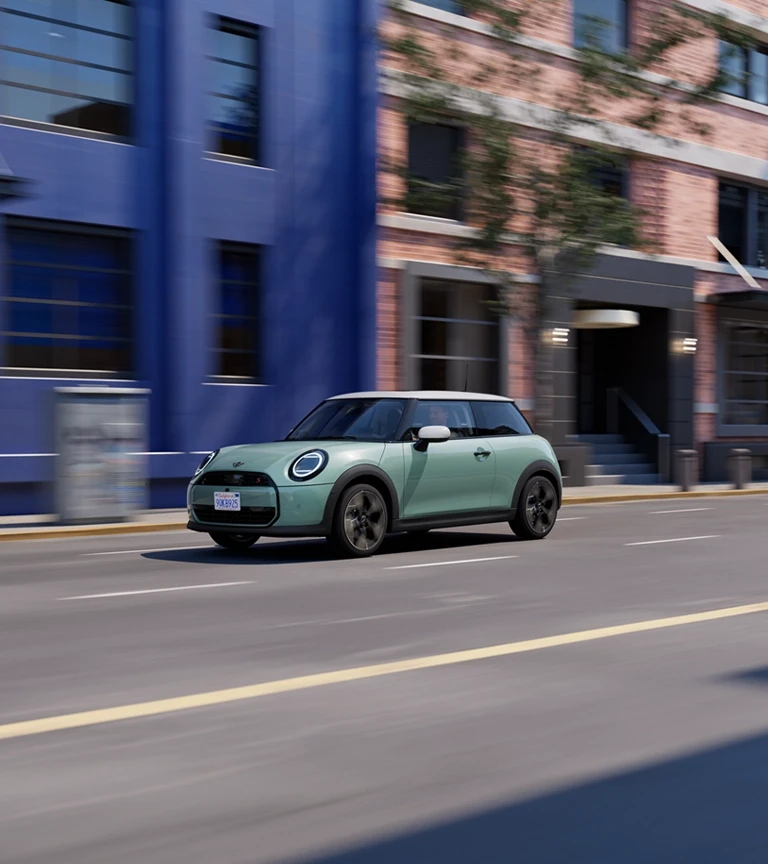
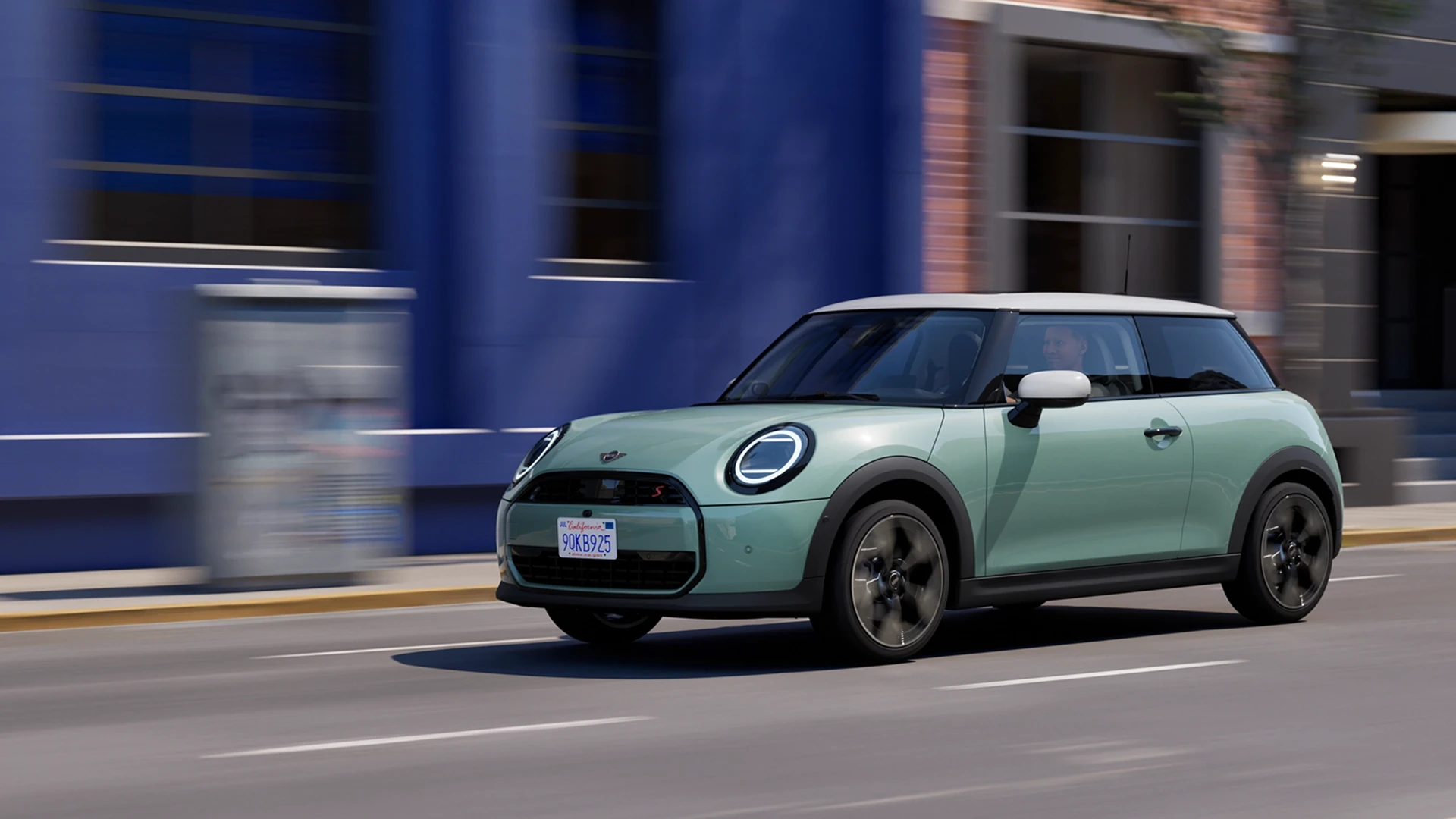
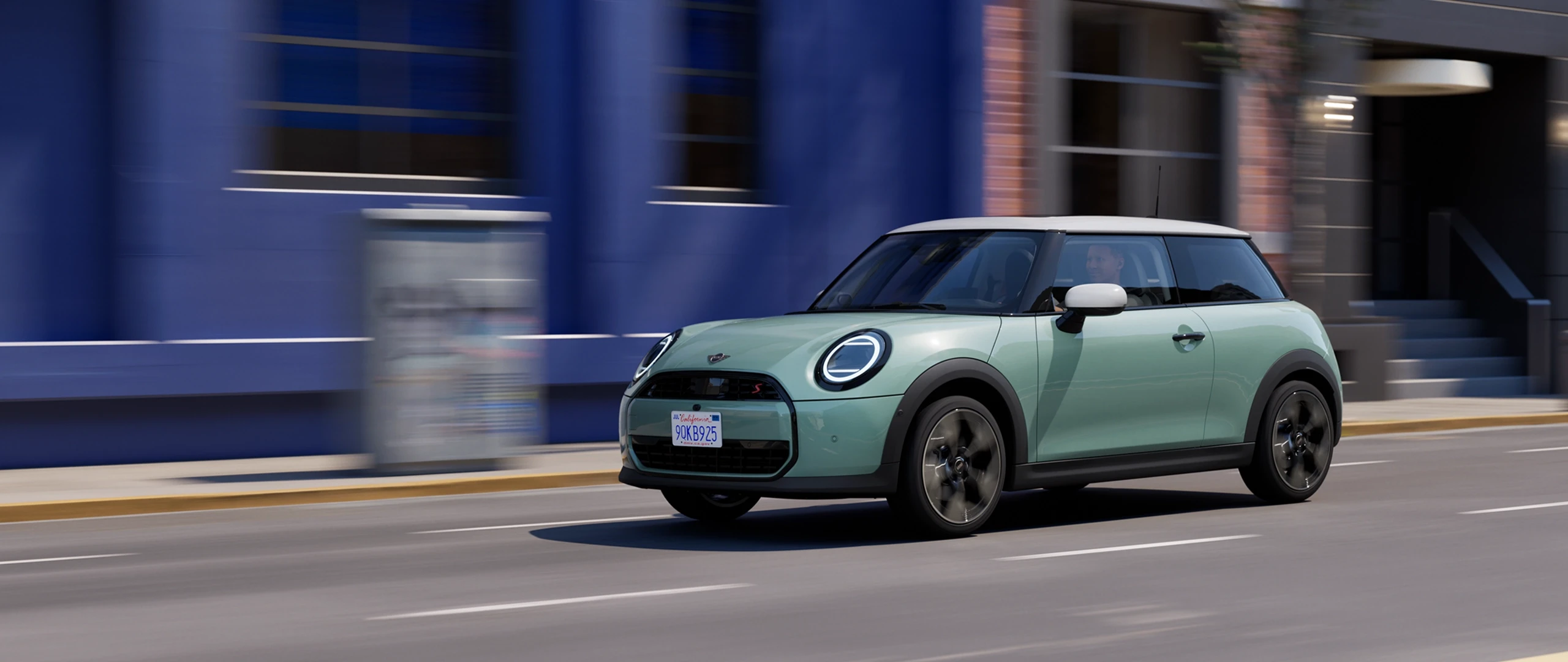
MINI COOPER.NICE TO MEET YOU AGAIN.
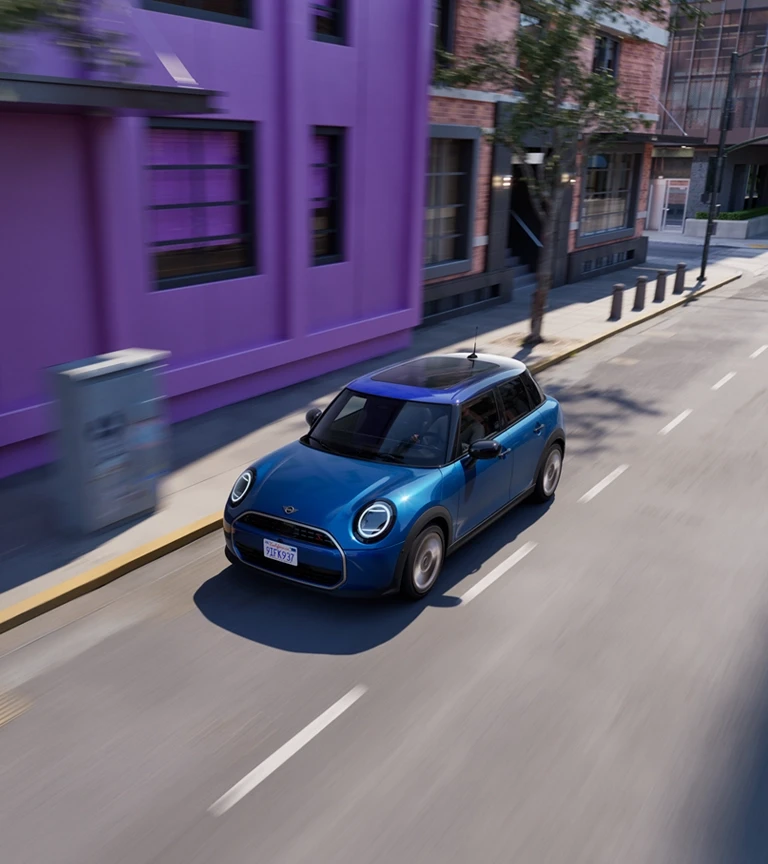
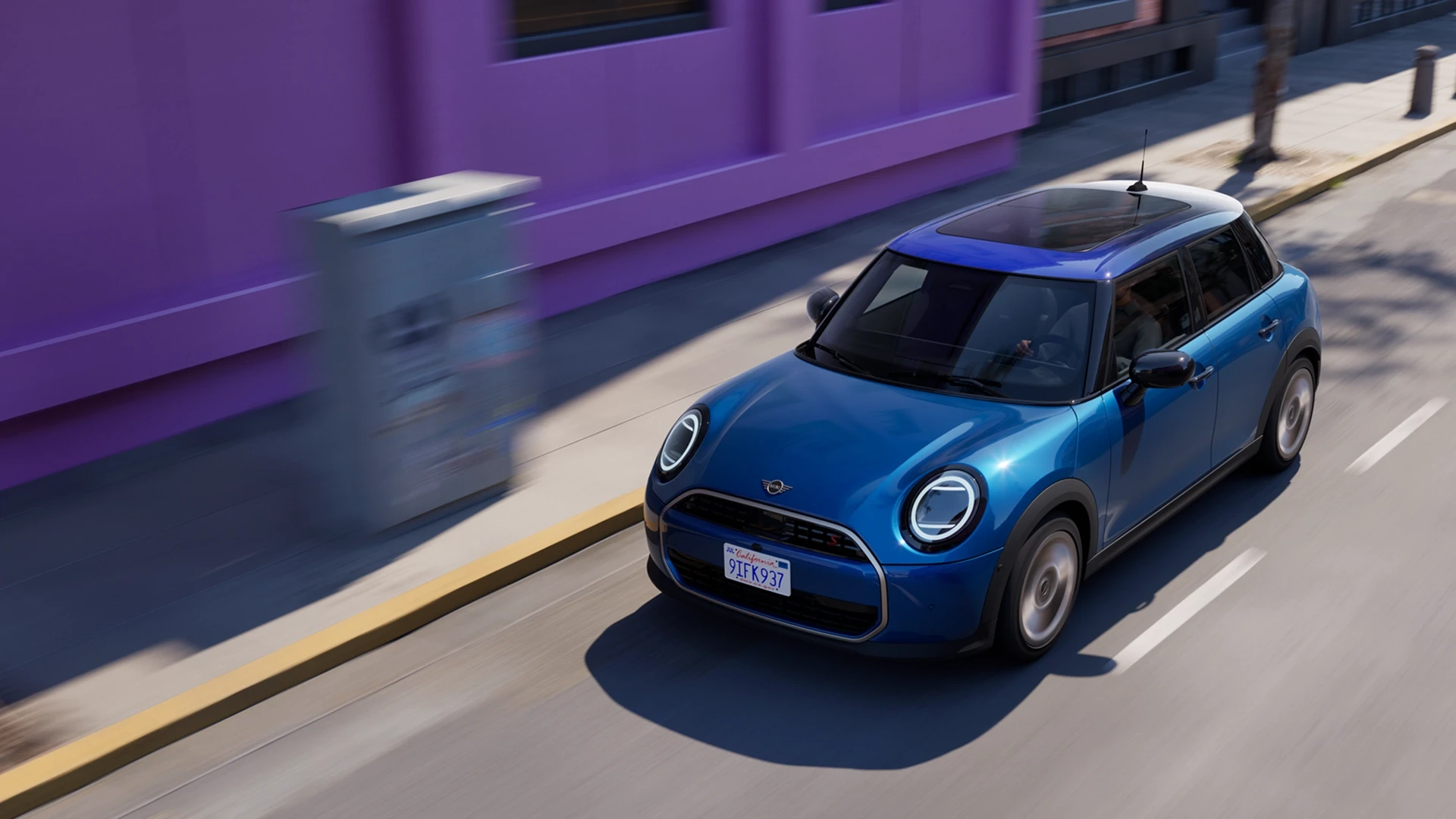
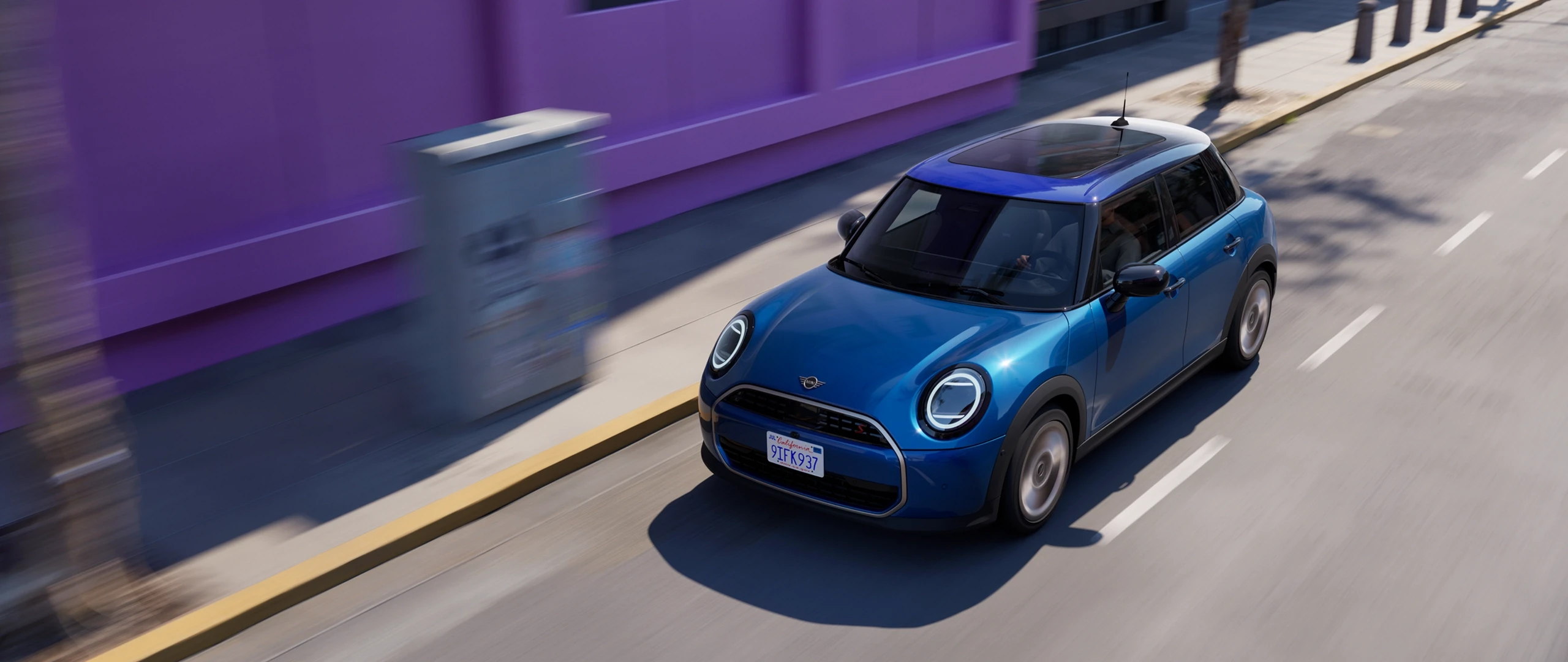
MINI COOPER 5-DOOR.NICE TO MEET YOU AGAIN.
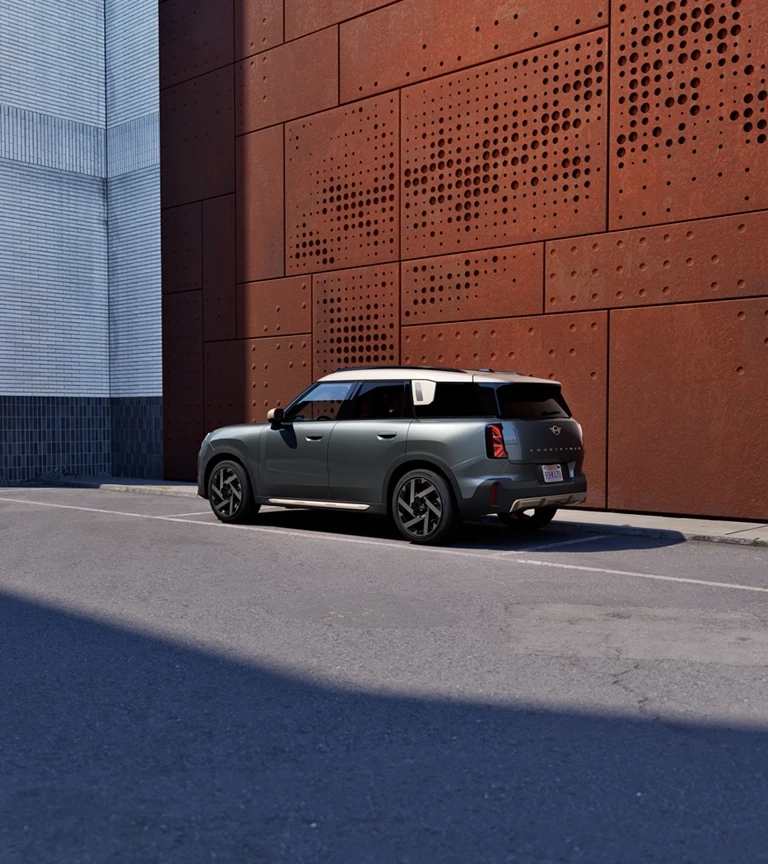
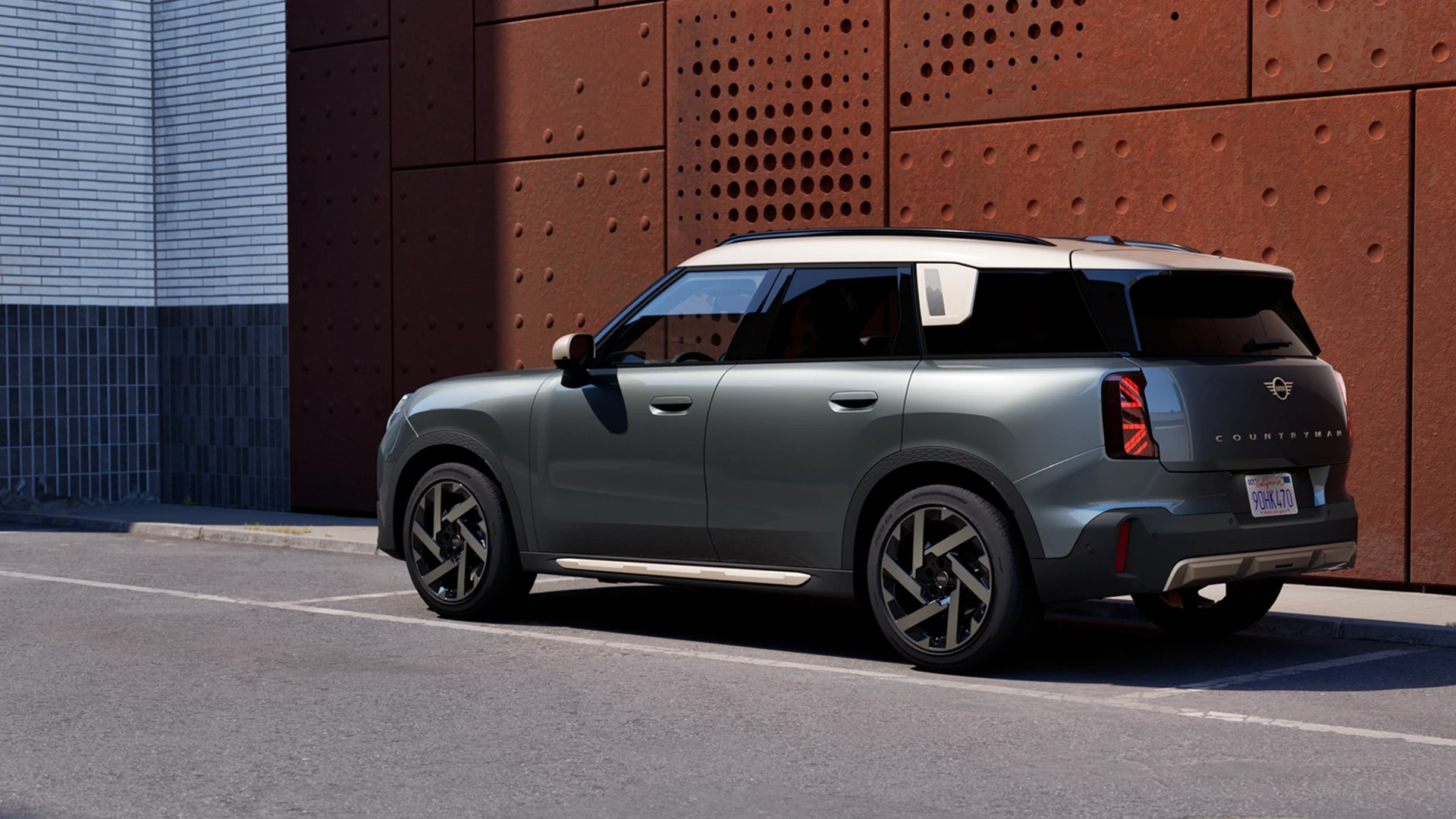
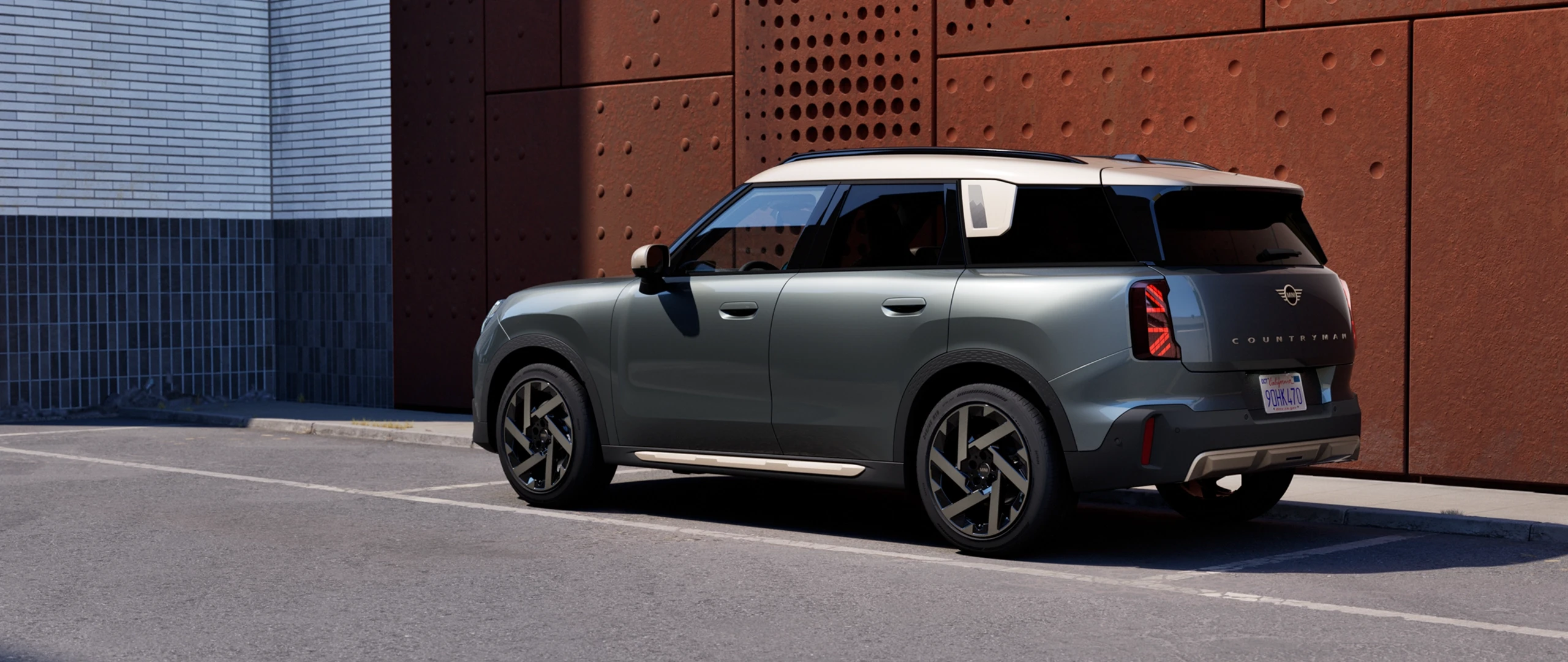